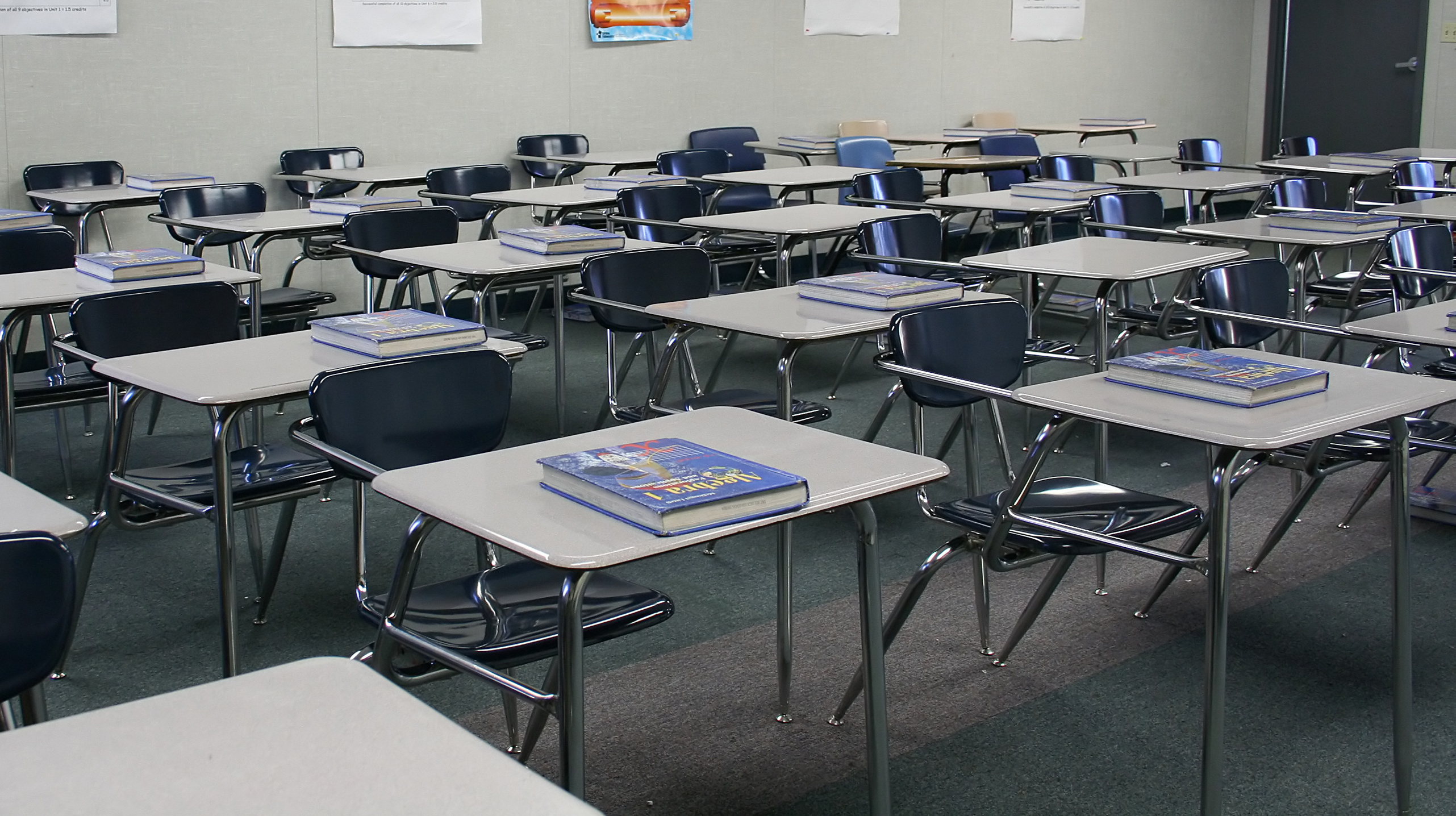
A unique, hands-on study, called the study, documents how one Florida school district’s Plant Manager’s Executive Committee (PMEC) developed a radical, high performance program that turned commercial carpet maintenance & cleaning wisdom on its head. The pay-off has been huge; and it repeats every year.
Their management model drives everything they do. It defines an approach to custodial services that sets the stage to engage opportunities as well as problems. Their carpeting system will work well in maintaining any type of commercial facility. The District’s model is not a straight line of point A to point B. Rather, it is a series of steps. Each step leads to the next in an ever repeating cycle: organize & identify, test, gather data, decide, fund, get buy-in, train, implement, monitor and assess.
Following their model, the PMEC realized that what they were doing to maintain their carpeting was in fact causing the poor appearance and costly extra work. – “We started this whole carpet research program because we were working too hard to make only marginal, temporary improvement” (District Custodial Services Coordinator). They discovered that to keep the carpeting looking new, they “deep clean” the traffic areas several times a week rather than simply “vacuum”… and at far less cost than what they had been doing.
This is an in-depth report of the 6 year District PMEC study. Their study, implementation and results were documented in a 9 month audit by HOST representatives. In the study you will learn how the district overcame “uglied-out” carpeting, doubled to quadrupled the attractive life cycle of it and delivered spectacular savings to the District. Using the HOST® System and the unique pile lift/extract/vacuum power of the HOST ExtractorVac®, they are able to do deep cleaning every day, yet the carpeting is dry for immediate use. The schools achieve their appearance and health objectives – without the complications associated with wet methods.
The study features hands-on supervisors sharing how they manage the maintenance & cleaning challenges that all types of facilities face every day:
- How to manage keeping new carpeting clean, cost effectively, from day one.
- How to restore and save old, filthy-dirty carpeting, and keep it in service without complaints from those who must use it every day.
- How to manage disasters such as floods from HVAC and other sources quickly and effectively.
- How to keep heavily used areas spotless…with minimal or no use of chemicals.
- How to implement a new maintenance strategy that will get buy-in from the wide variety of operating personnel in any organization.
- How to test and specify products and equipment in a way that insures the budget dollars will always be there from budget decision makers.
- How to satisfy the desire to “clean green”, conserve resources and keep environmentally burdensome materials out of the landfill and wastewater out of the treatment facilities.
The study indicates that hybrid resilient carpeting saves the school district $1.06 million in avoided maintenance costs every year vs. Vinyl Composition Tile (VCT) maintenance, if all areas were VCT. It costs the district $440 more per 1,000 sq. ft. per year to maintain VCT than carpeting. Data collected during an initial district-wide, four-year cost study indicate that, one elementary school spent 36 cents per sq. ft. annually to maintain 29,000 sq. ft. of 7-year-old carpeting in an “as new” condition. Assuming the lowest custodial labor rate, this adds up to a cost of $10,440 each year. The District Coordinator has said conventional wisdom holds that HOST is expensive, but don’t believe it. To restore carpet to the high level of clean that we do with the HOST system, given the same circumstances, the same dirty carpet, wet extracting is going to be more expensive, no question.
Here are a few of the insights:
Budget Implications
The study data indicate a cost of 80 cents per sq. ft. to maintain VCT (not including stripping). If the same 29,000 sq. ft. were covered in VCT, the maintenance cost to the elementary school would be $23,200per year. Avoiding VCT maintenance costs saves one school $12,760 per year: $23,200 to maintain VCT- $10,440 to maintain carpet using E-Vac & HOST= $12,760 savings, or 44 cents per sq. ft. cost avoided per year.
Extending Life Cycle Expectations for Carpeting
Carpeting as maintained in these facilities will last for 25-35 years, attractively and healthfully. Typical industry expectation for school carpet life cycle is reported to be 8-12 years. Just doubling the life cycle of carpeting offers enormous savings and conservation of resources. Avoided costs and realized conservation include premature replacement, land-fill, recycling and re-manufacturing.
“Architects and engineers typically haven’t liked carpet because where it has been put in their buildings they come back three years later to find it looks terrible. We’re changing that. But it’s the mind set. If you don’t do what it takes to maintain carpet, including things like adding carpet tile track-off inserts at entry ways, it will get ugly.”
-District Coordinator
Maintenance Strategies
The key to the high performance system is the E-Vac and its combination pile lifting/vacuuming design. This has more to do with the results than the cleaning material alone. It has a whole lot to do with the technology and the mechanical action. The only way to clean from the bottom up is with the Liberator or Freestyle E-Vacs.
“My maintenance strategy is `start from outside; work your way in. I’m pretty consistent about saying ‘this is how we do things.’ The people that work with me understand when I hire them that we do a set process.”
-Plant Manager
“I like to deal with carpet because with HOST I can do daytime cleaning. During the school day when my teachers go to lunch, they automatically go to recess. So, they’re gone for 55 minutes. In 55 minutes with time to spare, I can come in and extraction-vacuum with the Liberator (E-Vac). I can also use HOST SJ or HOST Spot Remover to clean up spots in two of these rooms. When they go to physical education, they’re gone for 40 minutes; so I can do the other two rooms, also during the daytime. So I’m actually cleaning carpet at a rate of about 2,500 sq. ft. an hour.”
-Plant Manager
Training Programs
Set up sessions to do hands-on training. The District Coordinator would bring people in and show them how to use the Liberator. The first meeting was at night on their own time, then they brought some administrators in to see the Liberator. Administration thought it was really good and eventually approved to allow cleaning on company time, during the regular work day.
“In training I hit hard on daily carpet spotting, even a microfiber cloth dampened with HOST Spot Remover or just plain water. 80 percent of the spots we see on a daily basis are still on top of the pile for the most part. Microfiber actually grabs and physically takes the spot out.”
-District Coordinator
“Asking if something works under real world conditions is another way to ask if it’s sustainable. We always look closely at what we’re doing, at what’s new and different. We want to find what works in the real world. In the case of HOST, we found nuances that will make it work or fail. If you let the machine get filthy or the filters are clogged, you’re going to have problems.”
-District Coordinator
Changing the Status Quo
When using wet extraction, one of the issues is wick back. They would spend days and days trying to make spots go away without much success, as well as odor issues from the wet cleaning and would only wet extracted once a year. It’s hard to believe that even today the standard in many schools around the country is that they wet extract just once a year, which means that their carpet is dirty most of the year.
“At a meeting in 2004, a group of our Plant Managers discussed carpet-related issues. We found that we all were encountering many of the same carpet cleaning problems such as severe wick back or browning, streaking reoccurring spots, fast soiling and poor overall appearance. This is what started our study.”
-District Coordinator
“I would never use hot water extraction, given a choice. I mean if it was all I had to work with. I’ve got a wet extractor here, but the only time I use it is as a wet vacuum when I have to clean up some sort of bodily fluids. If its just a spill of water or something that’s not real dark, I’ll just let it dry and take it out that night with the E-Vac machine. If it’s a coffee stain, depending on the size of the spill, we use several methods from wet vacuuming to just blotting the spill dry and using microfiber cloths. Dry coffee spots are treated by size. We use SJ and the Liberator on larger ones, but may only need HOST Spot Remover or plain water with microfiber cloths on small ones.”
Saving Flooded Hybrid Resilient Carpet
The media center’s 14-year-old sea foam green carpet was flooded with rusty water. For about a third of the cost of new carpet, they were able to restore what was there and the carpet is still in use today. They vacuumed the water with a wet vac, and went to work with the Liberator, HOST SJ, HOST Extraction Cleaner and HOST Spot Remover. They were able to remove all stains and make its appearance acceptable, even visitors have said it looks almost new.
“We spent a lot of time and work, and it cost $2,695 for temporary labor in addition to school staff and 8 cases of SJ; for a total of $3,911. But we didn’t have to replace the 4,000 sq. ft. of carpet at $23 a sq. yd. Replacement would have cost $10,222.”
-District Coordinator
Restoration of 25-Year-Old Hybrid Resilient Carpet
The school’s media center is seldom empty. The room is so tightly scheduled that time for maintenance is limited. A custodian described how the center’s once uglied-out, burnt-orange carpet installed when she was a student there over 30 years ago, was brought back to life using HOST.
“When we began this restoration process, we just E-Vac’d with the Liberator. Moving along in just one direction, in seconds that clear hopper was filled with sand. You could pretty much sit back and watch the hopper fill with sand. We E-Vac’d for a full day, until we were no longer dumping sand out of the hopper every 10 minutes. Then we applied HOST.”
-Plant Manager
“I’ve been using wet extraction for years, so the carpeting had gone from its original orange color to brown. Now, the original burnt-orange color is back”.
-Plant Manager
Indoor Air Quality and Green Cleaning
HOST sponges, already contains 1 teaspoon of liquid per square foot of carpeting cleaned; that is 0.167 fluid ounces. So if you calculate the amount of moisture used to clean 1,000 sq. ft. with HOST, it comes to 5.2 quarts. By contrast, hot water extractors are designed to use from 17 to 167 gallons of water per 1,000 sq. ft. cleaned. Typical wet extractors would use 1,500 gallons of water each time the 29,000 sq. ft. of an elementary school is cleaned. HOST cleaning uses no local water. The impact of the water use factor will vary by region.
According to the District’s Cost study, it would cost $580 for the energy needed to dry 29,000 sq. ft. of carpet cleaned using a wet extraction method. This assumes a single cleaning per year and that the carpet could be dried in a 24 hour period. Should a second wet extraction be needed, energy costs would double to $1,180. Running the Liberator for 8 hours consumes the power of a 100 watt light bulb burning all night.
“The media centers have dehumidifiers and run 24/7 because it is Florida, and there’s a lot of moisture to trap. You can imagine what this means if you’re wet extracting carpet in terms of energy use. When we used to wet extract, we’d have to run the air conditioning to dry it, and that took a long time, a lot of energy.”
-District Coordinator
“In one classroom in particular parents complained that the carpeting was aggravating their child’s severe allergies. So, we used the Liberator daily for 3 weeks. The end result, the child’s allergies were no longer aggravated, the parents were pleased and the problem was solved.”
-District Coordinator
Grouted Tile Floor Applications
“We use Sponges and the E-Vac with red brushes on the grout in a few bathrooms. One school is old and it had pink grout. The grout that wasn’t re-grouted is getting its pink color back again.”
-Plant Manager
- Get Organized: Buy-in from management allows you to organize and take on tasks. Organization gives you credibility with purchasing, which is key to getting the products and equipment you need to implement change.
- Identify the Problem or Need: There is probably a better way to do what you are charged to do – less expensively, more environmentally friendly. Identifying an issue is the starting point for gradual, continual change.
- Conduct Research and Test Models: Find and consult with other organizations that are doing the things you would like to do. Test your alternatives for efficiency, repeatability and validated results.
- Gather Data: Numbers can help you clarify what’s involved in implementing new systems and determining where they add value – or not – to your processes.
- Make Decisions: Once you have the information you need, it’s time to draw up a plan and make your decision.
- Request Budget: Your thorough preparation before preparing a budget sets the stage for purchasing to trust that your request for funds deserves approval.
- Orient Users to Get Buy-in: Let those who will be implementing the changed processes and procedures know what is coming, they need to be informed and involved in the process up front.
- Implement Training: Hands-on training is key to the successful introduction of something new – for those who will be working with these materials and administrators as well.
- Implement Monitor/Re-train/Get Feedback: Follow up. Re-train. Are the changes accomplishing expected results? Are those responsible for implementing these changes having problems? Why? What can be done to fix the situation?
- Assess; Is a Product or Process Sustainable: What works in testing may not be sustainable under “real world” conditions. Keep on top of the changes you implemented and all possible problems, including ongoing training.